01 Overview
Different types of steering systems are applied to the front suspension to achieve front-wheel steering in vehicles. Four-wheel steering (4WS) enables rear-wheel steering based on front-wheel steering, while rear-wheel steering alone is typically used in engineering vehicles like bulldozers and lawn mowers, allowing larger steering angles and smaller turning radii.
For passenger cars, rear-wheel steering has several drawbacks:
1.Vehicle handling becomes unstable at speeds exceeding a threshold, making steering control difficult and increasing the driver’s workload—especially at high speeds, where the vehicle is nearly out of control.
2.Regulations require steering systems to have active self-centering capability at any speed, which rear-wheel steering vehicles lack.
3.When moving forward from a parking space, the wheels are prone to hitting curbs.
Due to these reasons, passenger cars and trucks generally adopt standard front-axle steering. The first four-wheel steering vehicle was a Mercedes-Benz transport vehicle (107VL) produced in 1936, but only 42 units were made and delivered to the Nazi German army.
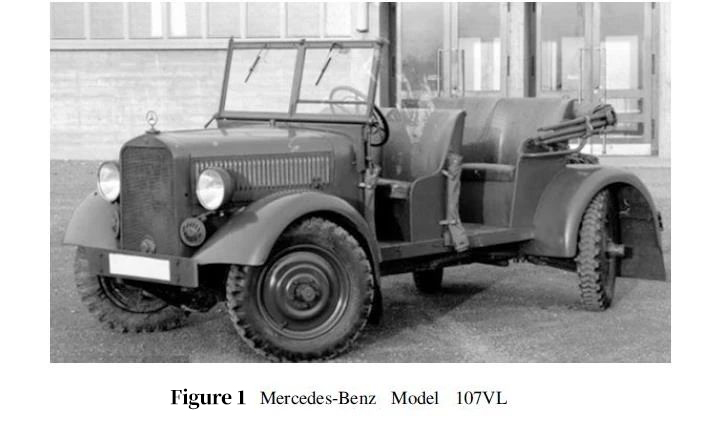
In recent decades, four-wheel steering has been applied to different types of vehicles. Nissan developed a four-wheel steering system in 1980. The types of four-wheel steering vary according to different power forms. Next, we will introduce the classification of four-wheel steering in detail.
02 Classification of Four-Wheel Steering
Rear-wheel steering can be divided into three types: mechanical, hydraulic, and electric.
2.1 Mechanical Four-Wheel Steering
The mechanical four-wheel steering system has a connecting mechanism between the front and rear wheels, which is shaped like a drive shaft. The steering angles of the front/ rear wheels are relatively fixed. The mechanical four-wheel steering design of the Honda Prelude model:
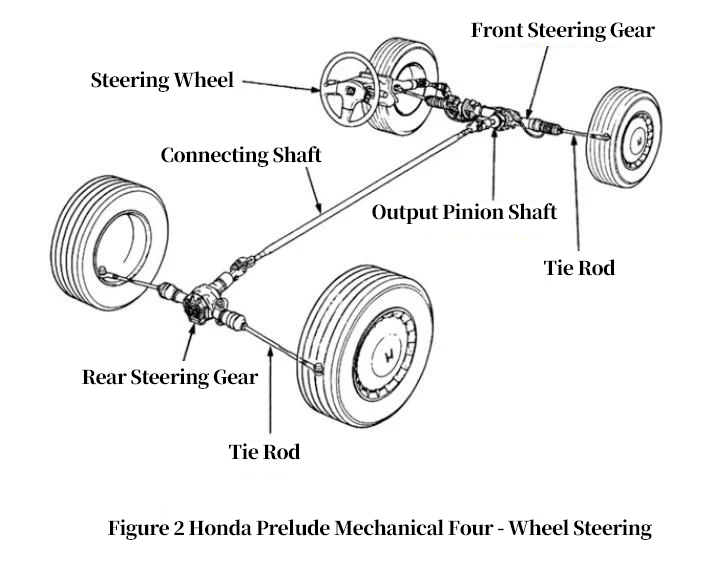
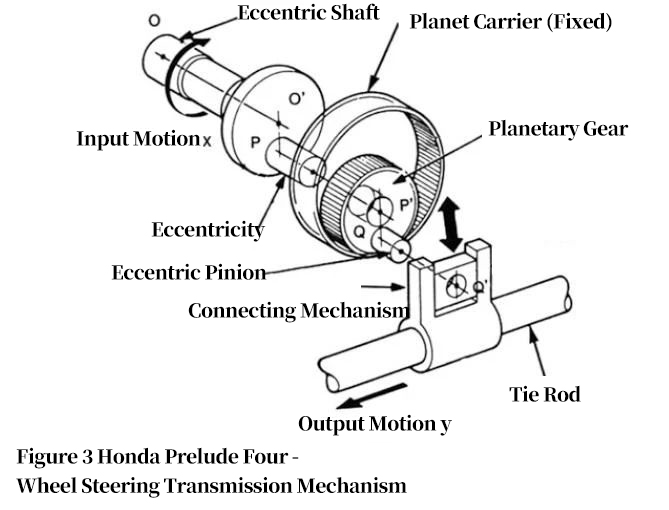
When the vehicle steers at a small angle at high speed, the rear axle steers in the same direction as the front wheels, which can increase the vehicle’s stability because the yaw is small. When the vehicle steers at a large angle at low speed (exceeding 127°), the steering transmission structure makes the rear wheels turn in the opposite direction to the front wheels, which can improve the vehicle’s maneuverability at low speeds. When the steering wheel angle is 450°, the rear wheels achieve a maximum steering angle of 5.3°.
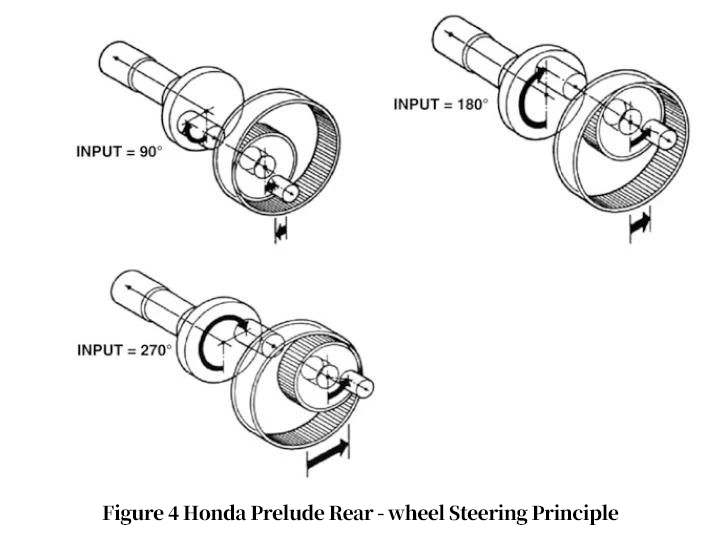
This mechanical four-wheel steering has design flaws: when the steering angle is small, the rear wheels steer in the same direction, deteriorating maneuverability. When the steering angle increases, the rear wheels steer in the opposite direction, causing the vehicle to tend to oversteer. Therefore, Honda developed an electric four-wheel steering system for the Prelude model in the 1990s to address the defects of the mechanical four-wheel steering system.
2.2 Hydraulic Four-Wheel Steering
The first application of a hydraulic four-wheel steering system was Nissan’s HICAS (High Capacity Actively Controlled Suspension) system. However, Mitsubishi Gallant’s hydraulic four-wheel steering was mass-produced in multiple factories in 1987, making it difficult to determine which automaker first applied hydraulic four-wheel steering. The hydraulic four-wheel steering arrangements and structures adopted by these two automakers are similar, consisting of a hydraulic pump, pipelines, oil reservoir, actuators, etc.
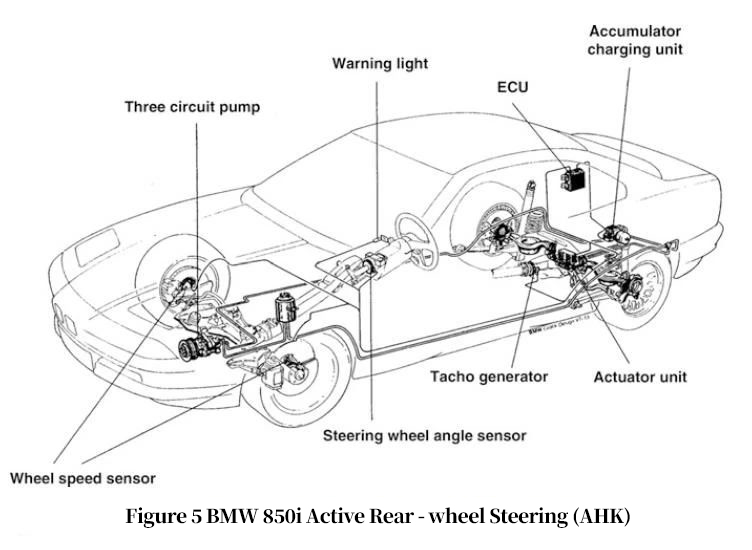
The BMW 8 Series first adopted an electro-hydraulic controlled active rear axle for four-wheel steering in 1992. The purpose of developing the active rear axle was to improve vehicle steering safety during maneuvering. The active steering function of the active rear axle requires controlling the lateral forces exerted on the wheels under high lateral acceleration. A hydraulic four-wheel steering system can be divided into three subsystems: hydraulic power supply and actuators, system control, and detection systems.
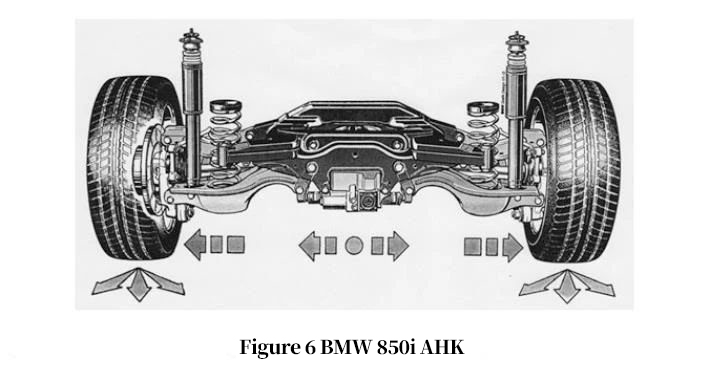
2.3 Electric Four-Wheel Steering
To address the complexity of hydraulic four-wheel steering and the performance defects of mechanical four-wheel steering, electric four-wheel steering was developed. Electric four-wheel steering offers the following advantages:
- The rear wheels can steer at any angle independently of the front wheels;
- Simple structural arrangement;
- Lighter weight;
- The impact of system failure can be minimized.
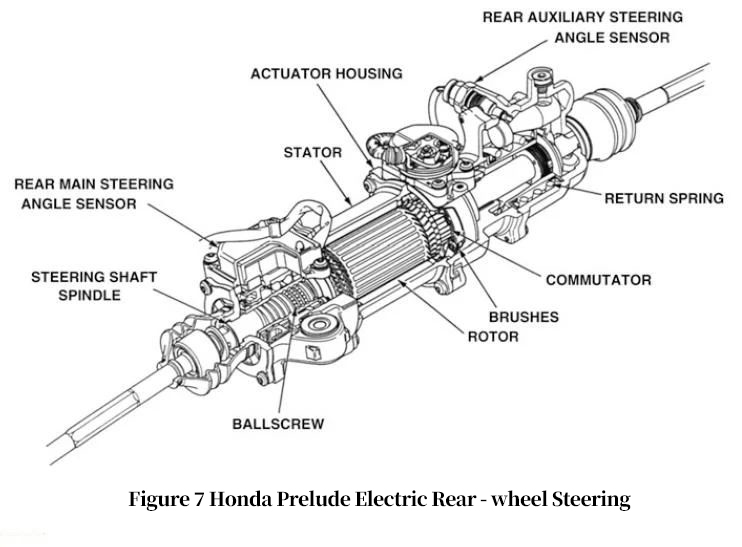
Electric four-wheel steering is driven by an electric power assist unit. The ECU calculates the torque and stroke that the assist motor should output based on input values. (Compared with brushed motors) Brushless DC motors are mostly used, which have no wear and are easy to control for safety systems. Sensors detect the correct position of the motor, and the rotational movement of the motor is converted into the lateral movement of the rack through the transmission mechanism.
The electric four-wheel steering system provides more possibilities for optimizing the dynamic performance of the rear axle. Any performance parameter values can be used as inputs, such as vehicle speed, steering wheel angle, yaw rate, lateral acceleration, etc. As mentioned above, Honda developed electric four-wheel steering in 1991. The above figure shows that the electric steering structure is very complex. The motor transmits torque to the steering shaft through a recirculating ball steering gear. For safety considerations, the electric four-wheel steering is equipped with a steering angle sensor. If the system fails, the rear wheels return to the central position by the return spring.
KYB has developed another type of electric four-wheel steering and applied it to Nissan models in the Japanese market. As shown in the figure below, the transmission mechanism transmits the torque of the servo motor to the rear wheels.
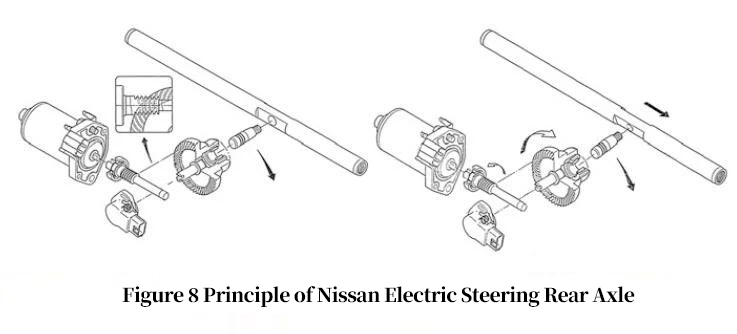
In the 1990s, almost all four-wheel steering systems disappeared from the market, mainly due to high costs and limitations in dynamic improvements. Another reason was that the ESP braking control system significantly enhanced vehicle dynamic performance at a relatively low cost, though the Japanese light truck market might be an exception. Before 2016, only three automakers used four-wheel steering in passenger vehicles: Renault Laguna GT (2008), BMW 7 (2008)/BMW 5GT (2009)/BMW 5 (2010), and Nissan Infinity FX50 and G37. Of course, many new automotive brands have revived rear-wheel steering as a marketing gimmick today.
The figure below shows the schematic diagram of electric four-wheel steering for BMW 5 Series and 7 Series.
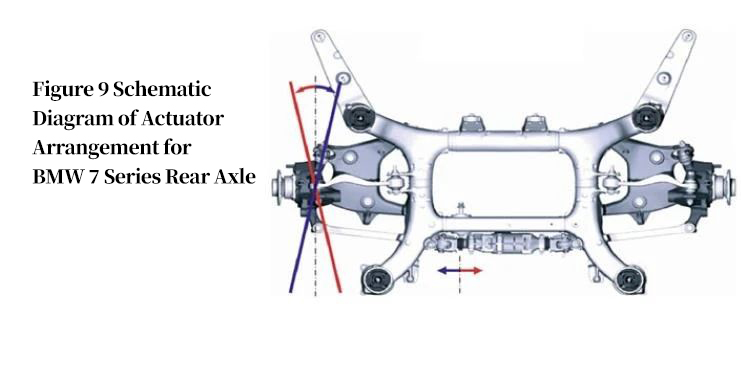
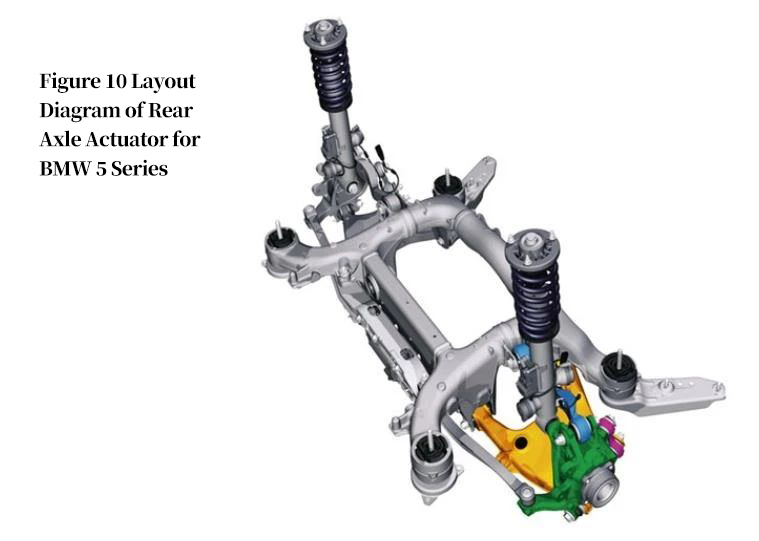
2.4 Central Actuators or Single-Side Actuators
Nissan, BMW, and Renault’s four-wheel steering rear axles all adopt central actuators, which are rigidly connected to both wheels via linkages, enabling the two wheels to steer at the same angle. Central actuators require continuous space from left to right, which is unfeasible for some vehicles. Therefore, single-side actuators have been developed, with similar products from ZF and Continental. The diagram below shows a schematic of a single-side actuator, which can independently control wheel toe-in, offering significant benefits for assembly and vehicle dynamics control.
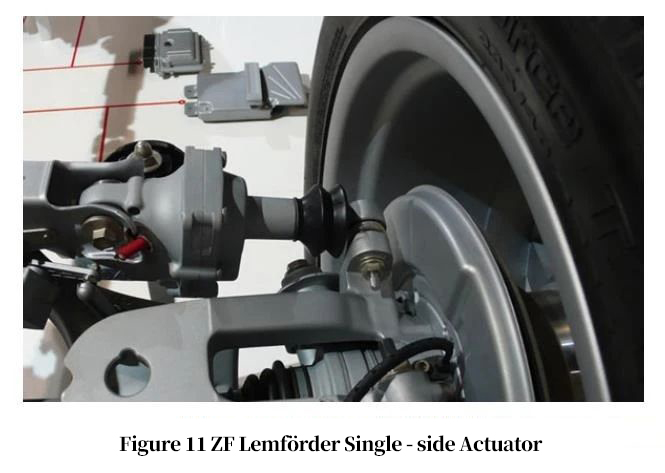
However, single-side actuators lead to an increase in the number of parts and costs. Moreover, the risk of system failure is doubled during operation. In terms of weight, single-side actuators are roughly equivalent to central actuators, with no significant difference.
03 Influence of Four-Wheel Steering on Vehicle Dynamics
The application of four-wheel steering systems aims to improve vehicle lateral dynamics control. First used in the 1930s to enhance wheel self-centering and vehicle maneuverability, subsequent developments considered improving vehicle response and driving stability.
- Mechanical four-wheel steering: The rear-wheel steering angle δh is a function of the front-wheel steering angle δv or steering wheel angle δH: δh = f(δv)
- Electric four-wheel steering: The rear-wheel steering angle δh is a function of vehicle forward speed vx and front-wheel steering angle δv or steering wheel angle δH: δh = f(vx, δv)
In the subsequent development of electric four-wheel steering, based on the application of dynamic sensors, it was expanded to consider yaw rate, longitudinal and lateral accelerations, etc.:
δh = f(vx, δv, △δv, δh, ax, ay, Ψ, β, …)
3.1 Kinematic Characteristics of Four-Wheel Steering
The coefficient kp is used to describe the ratio of the rear-wheel steering angle to the front-wheel steering angle in a four-wheel steering system:
kp = -δh/δv
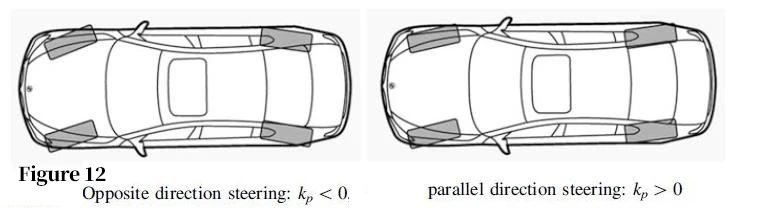
For four-wheel steering systems, discussions can be divided into two aspects: parallel steering and opposite steering:
kp < 0: Opposite steering
The rear wheels turn in the opposite direction to the front wheels. The instantaneous center of the wheel rolling trajectory moves forward, equivalent to reducing the wheelbase. This shrinks the turning diameter, but the rear axle changes its motion trajectory, making the vehicle harder to control and reducing maneuverability.
kp > 0: Parallel steering
The rear wheels turn in the same direction as the front wheels. The instantaneous center of the wheel rolling trajectory moves backward, virtually increasing the wheelbase to enhance vehicle stability.
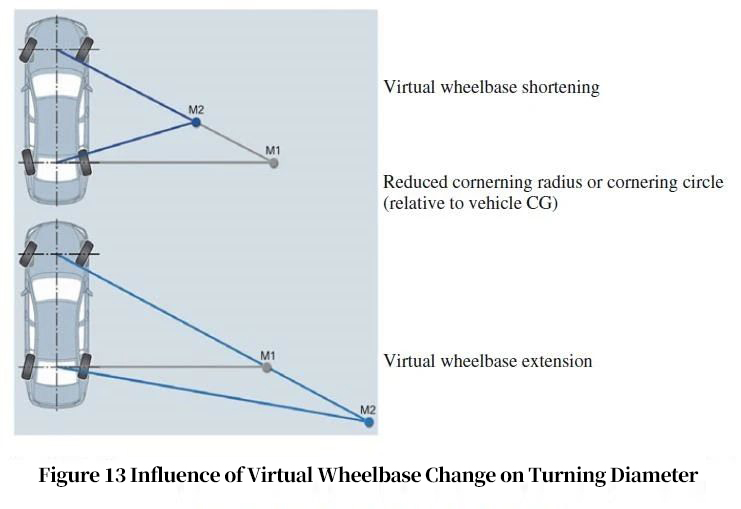
3.2 Influence of Four-Wheel Steering on Vehicle Steady-State Characteristics
The influence of four-wheel steering on vehicle steady-state characteristics should be examined through steady-state circular tests. The maximum achievable lateral acceleration of the vehicle remains nearly unchanged, but the yaw angle at the vehicle’s center of mass differs. If kp > 0, the yaw angle at the center of mass decreases due to the rear wheels turning at a certain angle.
In past development experience, kp is theoretically often designed to compensate the yaw angle of the vehicle’s center of mass to zero, aiming to achieve a stable driving state. However, modern theories have found that steady-state driving requires additional parameters, such as road surface change feedback and responses from the linear region to the limit region. Sometimes, the yaw angle is over-compensated by the rear wheel angle, causing the vehicle’s yaw angle to become negative at higher lateral accelerations, resulting in an increased tendency for understeer.
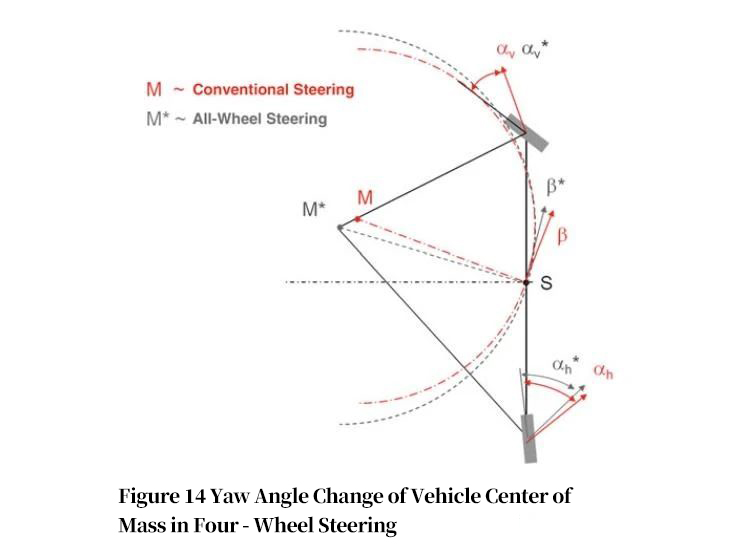
3.3 Influence of Four-Wheel Steering on Vehicle Transient Characteristics
The influence of four-wheel steering on vehicle transient characteristics should be examined through wheel angle input tests and ISO lane-change tests. The left view below shows that when a wheel angle is input, the vehicle rapidly and stably builds lateral forces on the front/rear axles, minimizing vehicle yaw, slowing the build-up of yaw rate, and accelerating the build-up of lateral acceleration. The functional curve of yaw angle versus lateral acceleration shifts downward, enabling drivers to experience better predictability and drivability at high speeds.
Contrary rear-wheel steering generates opposite initial lateral force build-up on the front/rear axles, leading to increased vehicle yaw and smaller initial lateral acceleration—achieving the desired better self-centering capability for low-speed driving. ISO lane-change objective tests demonstrate that four-wheel steering improves vehicle drivability. As shown in Figure 15, the vehicle obviously has a smaller yaw angle with less yaw angle oscillation, and both yaw rate and lateral angular velocity are closer to steady state (relative to the moment of angle input).
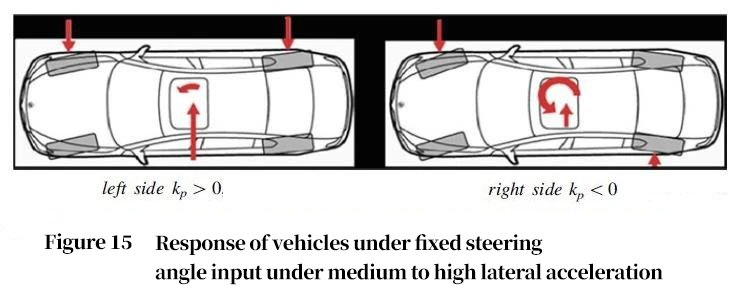
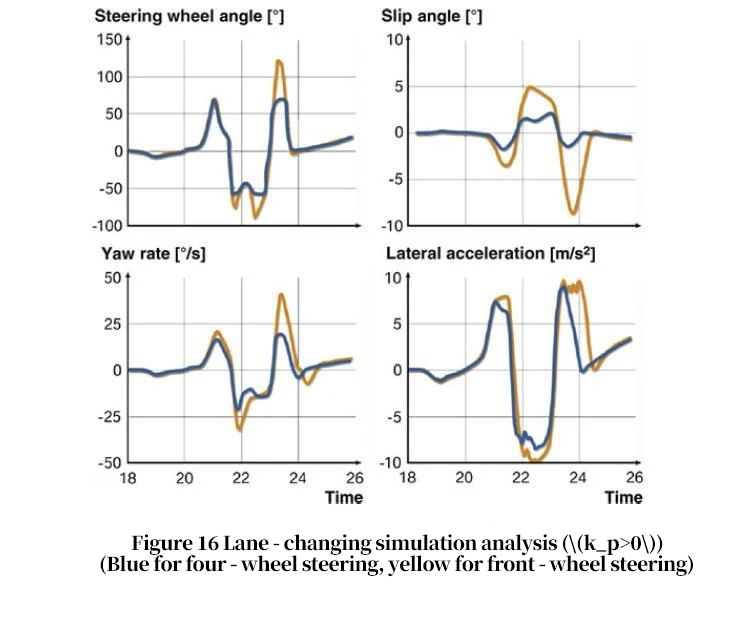
3.4 Integrated Active Four-Wheel Steering
This design allows the rear-wheel steering angle to vary based on vehicle speed and front-wheel steering angle. If the vehicle’s yaw angle is compensated to zero via a kp design, the vehicle exhibits a stronger understeer tendency relative to front-wheel steering alone. With the assistance of rear-wheel steering, both the steady-state and transient characteristics of the vehicle improve drivability. BMW was the first automaker to develop an integrated active steering system, known as Integral Active Steering (IAS). Figure 17 illustrates the hardware composition of the IAS system equipped on the BMW 5 Series. The rear axle electric steering unit combines with the front suspension electric steering system to form the hardware system, with ECU control integrated into the chassis ESP.
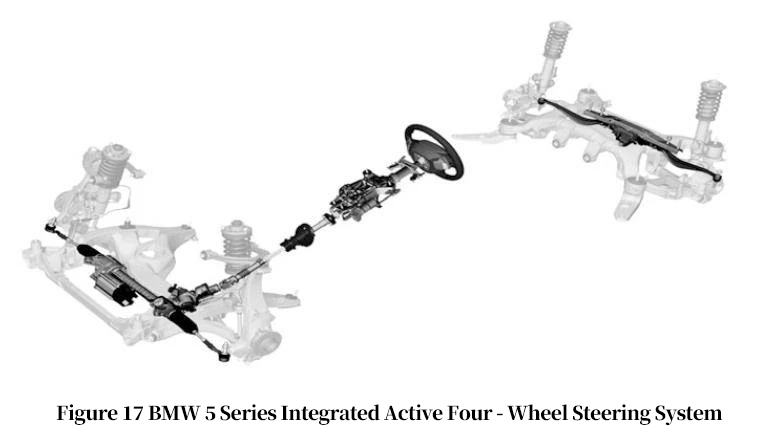
Nissan equipped the Infinity 37 with the 4WAS system in 2007, another integrated active steering system. This system operates at high vehicle speeds but remains inactive at low speeds. The front suspension electric steering system and rear axle electric steering unit can achieve different steering angles based on the driver’s input respectively. When the vehicle is traveling at low speeds, the integrated active steering system can realize a linear increase in yaw motion according to the driver’s input, making the virtual wheelbase smaller and the vehicle have better self – centering property.
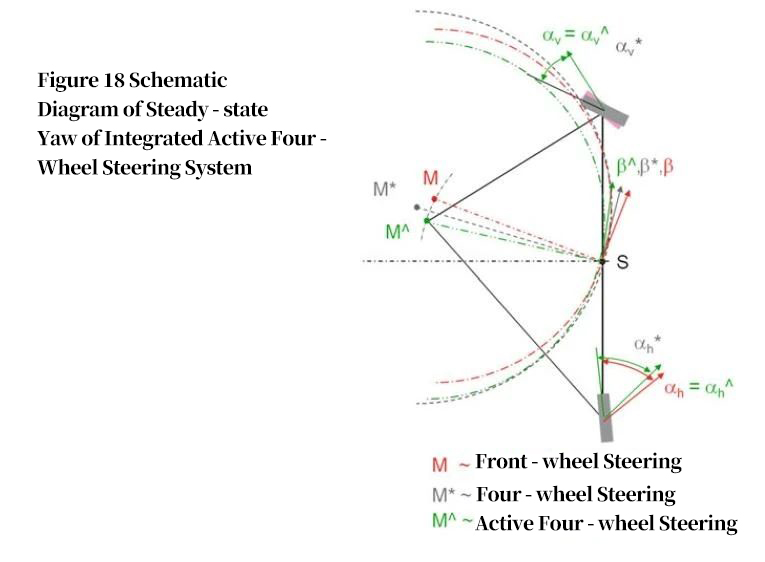
When the vehicle speed exceeds 50 km/h, rear-wheel steering collaborates with front-wheel steering. The steering angle increases continuously and is a function of vehicle speed and steering wheel angle. Figure 18 shows a comparison of steady-state yaw between a general vehicle and one equipped with integrated active steering under the same working conditions. The steady-state yaw can be expressed by the formula: Ψ = v/r. The steering wheel slowly and continuously increases until the vehicle reaches the limit lateral acceleration.
The front suspension electric power steering system works in coordination with the rear axle electric steering system. Like a general vehicle, the yaw rate builds up as the lateral acceleration increases. As previously mentioned, vehicles with integrated active steering have better driving stability. Under a maximum lateral acceleration of 8 m/s², the center of mass yaw angle of a vehicle with an integrated active steering system is half that of a general vehicle. Even if the lateral acceleration continues to increase, the yaw angle increases linearly. Four-wheel steering has opposite effects on drivability and understeer, requiring a trade-off in drivability design.
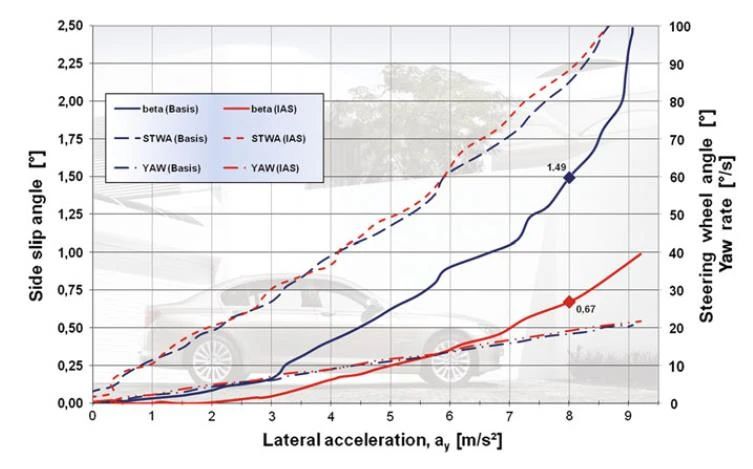