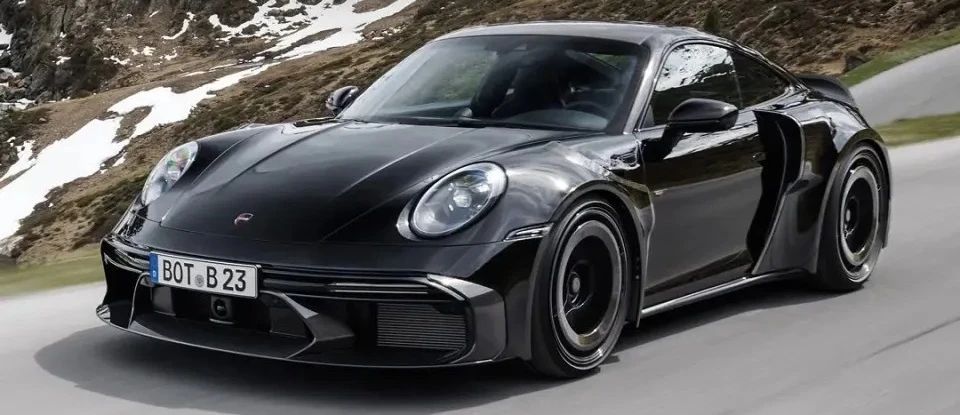
01 Abstract
A key feature of the new Porsche Carrera is its newly developed chassis, which offers driving enthusiasts with sporty preferences exceptional driving pleasure and active safety.The front suspension adopts a MacPherson strut design inherited from the previous generation but thoroughly optimized. Improvements in suspension geometry and kinematics contribute to enhanced straight-line stability and braking performance.The rear suspension features a newly developed lightweight multi-link system (“LSA suspension”), delivering maximum driving stability and agility. The integrated subframe significantly reduces tire noise.Both front and rear suspensions are equipped with internally ventilated brake discs and four-piston aluminum fixed-caliper braking systems.Following future-oriented lightweight construction principles, the new chassis utilizes aluminum components wherever technically and economically feasible.
02 Objective metrics
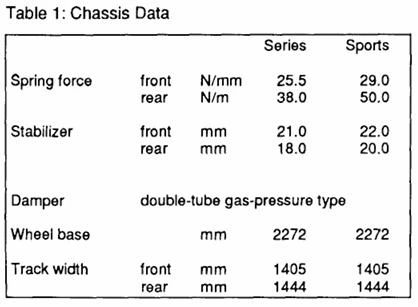
The following objectives were defined:
a) Outstanding active driving safety
※ Fast, direct, and precise steering response with clear feedback
※ Harmonious and safe lane changes even at top speeds
※ High lateral acceleration limits
※ Controllable acceleration and braking response during cornering
※ Minimal roll and pitch movements
※ High braking stability
※ Shortest braking distances on dry/wet roads, even after prolonged extreme stress
b) Tuning for sporty driving comfort
※ Fatigue-free long-distance driving
※ Significantly reduced tire noise
※ Low steering effort when parking
※ Reduced steering effort during rolling
※ Reliable foundation for everyday sporty driving
c) Weight reduction through lightweight materials and optimized design
※ Use of lightweight alloys and avoidance of bending loads in linkages
※ Reduction in overall vehicle weight, particularly unsprung mass
03 Front suspension
3.1Objectives
The proven MacPherson front suspension concept of the Carrera 2 and 4 (Figures 1, 2) must be retained while modifying kinematic parameters to further enhance straight-line stability on both smooth and uneven road surfaces, as well as braking stability under split-μ (different friction coefficient) conditions. Additionally, the front suspension weight must be reduced by replacing previous steel components with aluminum parts, thereby decreasing unsprung mass and optimizing front axle suspension characteristics.
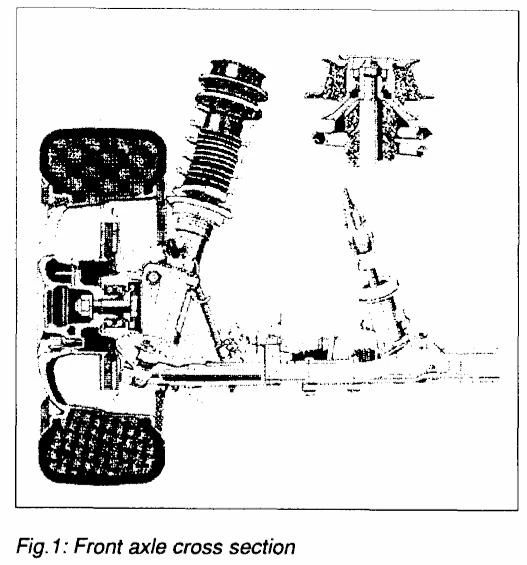
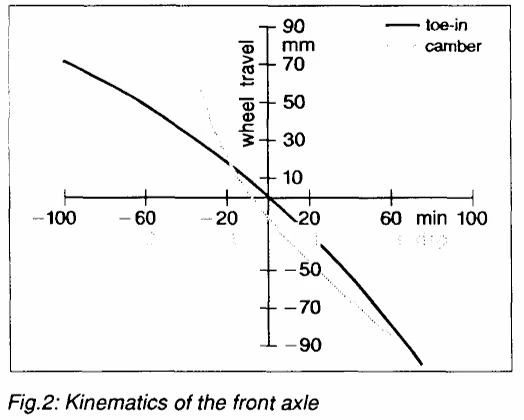
3.2 Implementation and Characteristics
Straight-line stability was improved by increasing the caster trail by 9 mm. Braking stability on split-μ surfaces was enhanced by setting the kingpin offset to -11.5 mm (compared to 0 mm in the previous model).To reduce unsprung mass in the front suspension, the steering knuckle was manufactured using low-pressure die-cast aluminum, achieving a weight reduction of 1.8 kg (47% lighter) compared to the previously used steel forging.When incorporating the already mass-produced aluminum components from the Carrera 2 and 4 into the front suspension, the steering knuckle assembly increased the aluminum content in the front suspension to 33%, including the braking system and wheels.
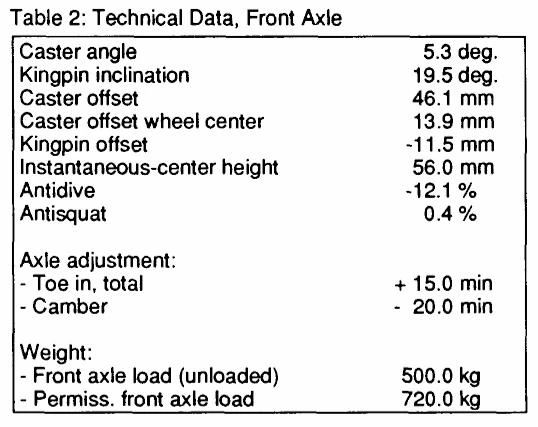
04 Steering System
4.1 Objectives
The following objectives were defined:
a) High vehicle agility and handling:
※ Responsive power steering reaction
※ Strong road contact feel with precise feedback
※ Low steering effort during parking
※ Precise yet relaxed response to steering inputs
※ Strict adherence to lightweight design principles through use of aluminum in steering system components
b) High passive crash safety:
※ Telescoping steering column
※ Measures to prevent steering wheel intrusion into passenger compartment
※ Crash-optimized steering unit/body boundary
※ Driver and front passenger airbags as standard equipment
4.2 Implementation and Characteristics
4.2.1 Steering
The hydraulic rack-and-pinion power steering system delivers exceptional road feedback while maintaining low steering effort, ensuring comfort during parking and urban driving. Direct, precise steering response—combined with roll and compliance steer effects—guarantees high agility. This agility, paired with sensitive reaction to steering wheel position in straight-line driving, forms a key criterion for active driving pleasure. To achieve this, the timing of the rotary valve in the power steering was recalibrated. The characteristic sporty agility of the Porsche 911 is attributed to its more direct 16.5:1 steering ratio.
4.2.2 Steering Linkage
Despite the highly direct steering ratio, harmonious response to driver inputs is achieved through newly developed elastic tie rods. Thrust bearings at the rack ends—featuring integrated rubber/metal elements and precisely defined stiffness—perfectly meet this requirement. Additionally, flexible joints help dampen impacts transmitted from the tires while reducing sensitivity to imbalances.
05 Rear suspension
5.1 Objectives
A new multi-link rear suspension with an integrated subframe (referred to as “LSA” – Lightweight, Stability, Agility) (Figures 3, 4) was developed to meet the following requirements:
※ Utilize all optimization possibilities for vertical and lateral vehicle dynamics
※ Improve kinematics and reduce unsprung mass
※ Enhance acceleration and braking response during cornering through compliant toe-in control
※ Improve ride comfort, particularly roll and chassis noise
※ Design for ease of assembly
※ Weight reduction
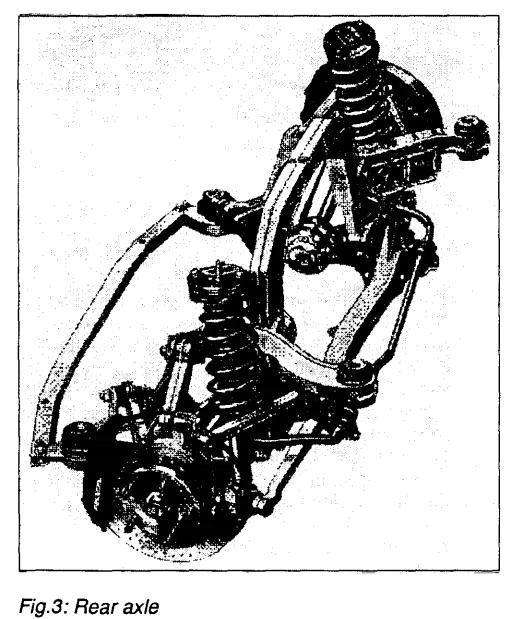
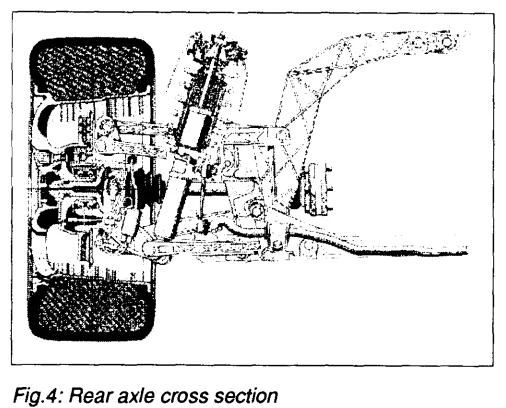
5.2 Implementation
The new rear suspension is a multi-link unit incorporating a subframe structure. The suspension consists of four links arranged across two horizontal planes. These links are compression/tension rods, connected at one end to the subframe and at the other to the knuckle. The links help reduce component stress while achieving weight reduction through dimensional optimization and lightweight materials.
This specific link arrangement ensures highly precise wheel alignment control:
※ The upper level comprises two rod-type links providing excellent anti-roll capability under lateral forces and reliable wheel control along the kingpin axis.
※ The lower level consists of one A-arm and one trailing link, ensuring precise toe control under both lateral and longitudinal forces.
※ The spring/damper assembly unit is supported at its lower end by the knuckle, while the upper end mounts to a bracket that independently absorbs spring and damping forces.
※ The subframe is mounted to the body structure via large rubber bushings for vibration isolation, with chassis forces transmitted to the body through wide mounting bases.
※ From inception, the suspension was designed to withstand high loads encountered in motorsports, requiring no component modifications for track use.
5.3 Lightweight Design
Lightweight design was a key focus from the conceptual stage of the rear suspension. In the early development phase, modern calculation methods and new manufacturing processes were employed to fully utilize the inherent material properties of each component.
The following objectives were achieved:
※ High component strength with low component weight
※ No need for imported materials
※ High recyclability potential
※ No corrosion or fatigue-sensitive welded joints
For the rear suspension and subframe, optimized manufacturing methods were selected considering all boundary conditions:
Subframe side structures, rear crossmember, and knuckle: Proven aluminum castings
Front crossmember of subframe: Aluminum extrusion
All links and upper crossmember of subframe: New aluminum castings
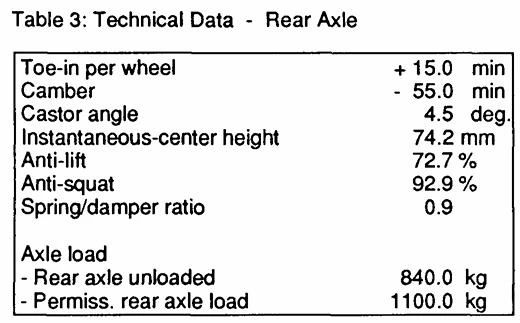
5.3.1 Die-Casting Technology
The proportion of aluminum in the rear suspension and subframe weight increased to 49%. By switching from steel to aluminum, some components achieved over 50% weight reduction. These measures significantly reduced unsprung mass.
5.4 Suspension Geometry Kinematics and Compliance
To balance the conflicting goals of optimal agility and stability, precise kinematic layout (Figure 5) and compliance characteristics were implemented. The kinematic virtual kingpin axis and compliant virtual kingpin axis of the wheel suspension have been separated (Figure 6). Links 1, 2, 3, and 4 are connected to the subframe via extremely rigid mounts, while Link 5’s mount is relatively soft.
Accounting for the elasticity of these mounts, the roll centers form along the extensions of the upper and lower links. These roll centers establish the compliant virtual kingpin axis, around which the wheel pivots under force influence. The virtual kingpin axis is positioned outside the wheel center plane and intersects the road surface behind the tire contact patch.
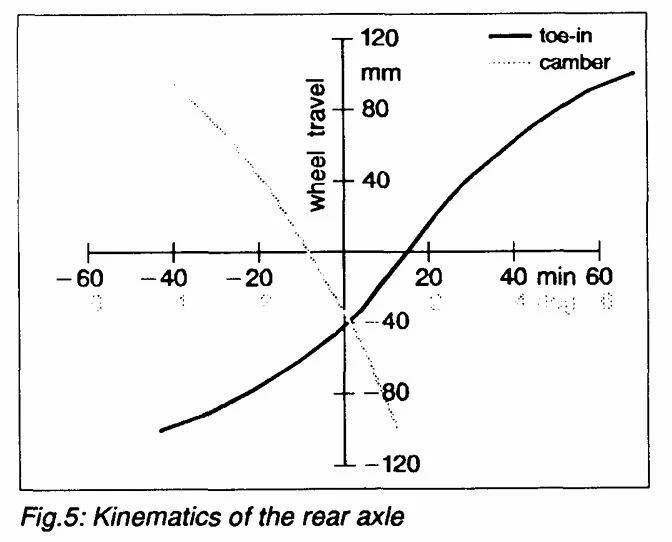
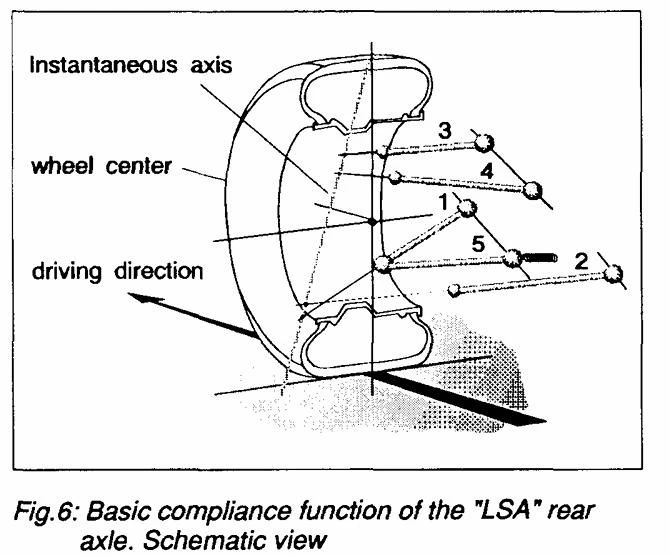
Under force influence, the resulting compliance-induced angle changes are as follows:
※ Driving/Braking Forces on Toe Angle:
Acceleration forces acting at the wheel center – combined with the lever arm between wheel center and kingpin axis – generate a torque that reduces static toe angle. Conversely, engine braking or wheel braking increases toe angle. This compliance-based toe adjustment evolves from the Porsche 928 rear suspension: during cornering deceleration/braking, the outer wheel tends toward toe-in, mitigating vehicle oversteer.
※ Lateral Forces on Toe Angle:
Lateral forces act at road level ahead of the kingpin axis. The resulting torque increases the outer wheel’s toe angle. Combined with the kinematic toe gain during compression, this ensures high stability during transient steering maneuvers.
The LSA rear suspension further improves deceleration response by redistributing roll stiffness. During loaded (accelerated) cornering, the kinematic anti-lift geometry generates internal forces between body and rear suspension, counteracting roll tendency – effectively increasing rear axle roll stiffness. During deceleration, this effect reverses: the front suspension assumes most roll moment, enhancing rear axle grip and driving stability.
06 Handling Characteristics
The handling characteristics of the Porsche 911 are demonstrated through objective testing. For comparison, measured values from various competitor models are also plotted. These values represent the latest state of the art.
6.1 Pitch Motion During Braking and Acceleration
To measure pitch, the vehicle undergoes deceleration and acceleration tests at varying speeds (Figure 7) to evaluate the chassis’ anti-pitch properties. Body pitch should be minimized as much as possible to ensure driver confidence and sporty driving comfort.
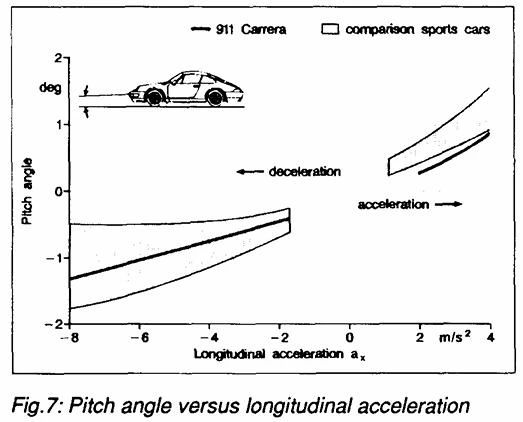
6.2 Steady-State Cornering
This maneuver characterizes the vehicle’s steering response under steady-state conditions. The Porsche 911 features a direct steering system requiring minimal steering wheel angles during steady-state cornering (Figure 8). Designed with inherent understeer, the steering angle initially increases linearly. As lateral acceleration rises, the steering wheel angle progressively increases. When approaching the limit range, the understeer tendency intensifies. The achievable maximum lateral acceleration reaches 0.93g (Figure 9).
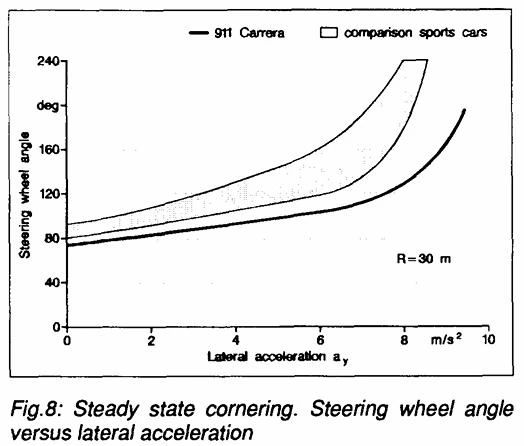
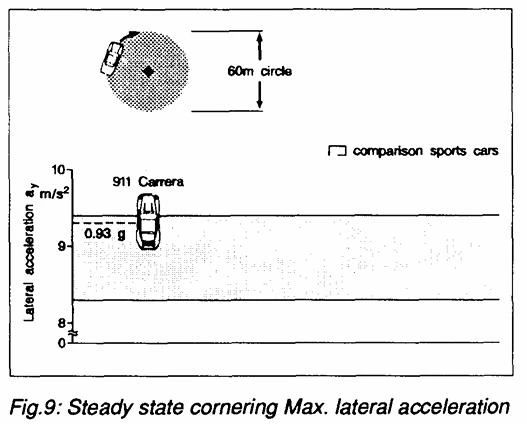
The Porsche 911 Carrera exhibits exceptionally low roll angles during cornering (Figure 10), with less than 3 degrees of body roll when lateral acceleration reaches 1g.
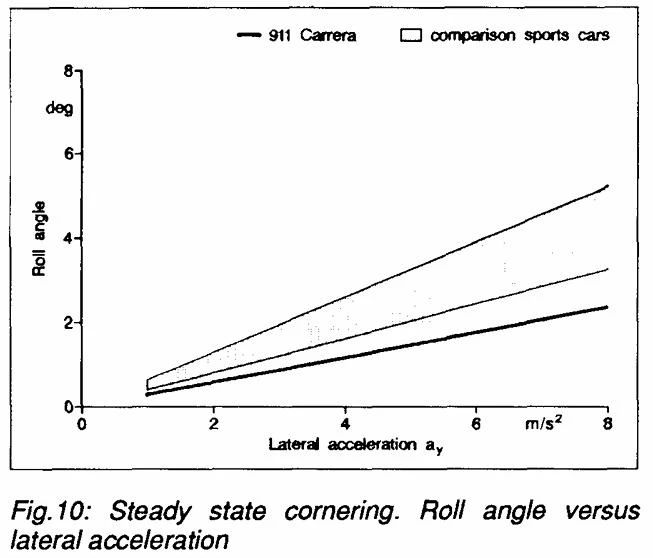
6.3 Deceleration During Cornering
Deceleration maneuvers provide insights into the vehicle’s cornering stability. Under high lateral acceleration, vehicles typically exhibit oversteer tendencies, which are mitigated through targeted chassis tuning.
Figure 11 illustrates the relationship between the measured yaw rate difference (after 1 second of deceleration) and initial lateral acceleration. Even under extreme lateral acceleration, the vehicle demonstrates negligible yaw response, with only slight oversteer emerging near the limit range. The yaw reaction remains so minimal that the vehicle maintains its curve radius effortlessly.
This exceptional deceleration behavior is achieved by an asymmetrically controlled limited-slip differential with:
25% lock-up under acceleration
60% lock-up during coasting
During cornering deceleration, the system counters oversteer by generating controlled force distribution between the rear wheels.
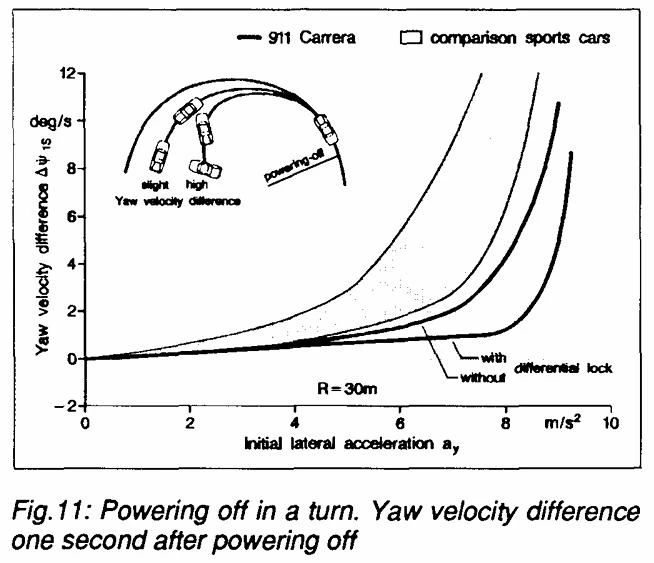
6.4 Braking During Cornering
Similar to deceleration maneuvers, this test evaluates the yaw rate difference within the first second after brake application. As shown in Figure 12, the vehicle demonstrates excellent braking stability during cornering. Only when longitudinal deceleration reaches between 6-7 m/s² does the vehicle exhibit slight oversteer tendencies.
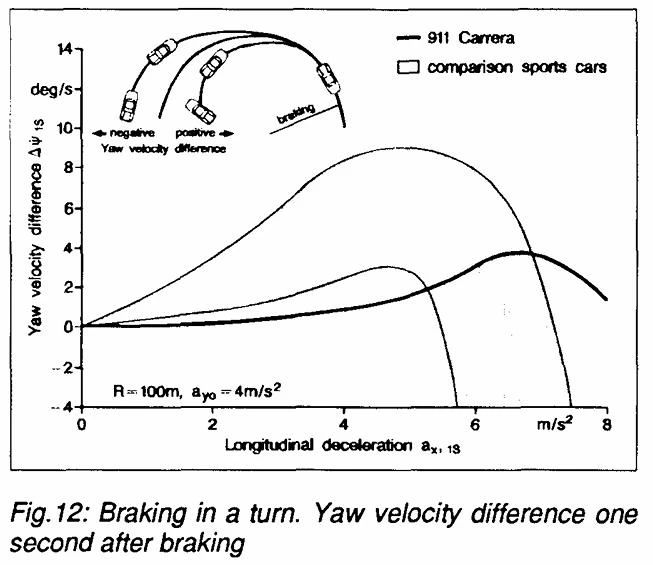
This outstanding braking stability is attributed to the compliant toe control of the new multi-link rear suspension described in Section 5.4. Under braking forces, the toe angle increases (Figure 13), generating an understeer moment that counteracts oversteer behavior during corner braking.
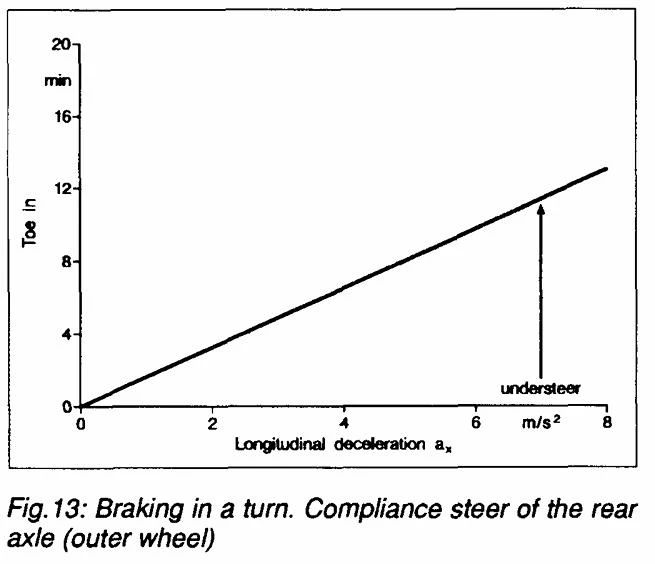
6.5 Lateral Dynamics
The vehicle’s lateral dynamics can be evaluated through slalom testing (Figure 14). On a 210-meter test course with cones placed at 30-meter intervals, the driver’s task is to navigate through at the highest possible speed. The tuning of both front and rear suspensions proves critical during this test—the vehicle must demonstrate neither excessive understeer nor compromised rear suspension stability. The Porsche 911 Carrera achieved a top speed of 106.5 km/h in this evaluation.
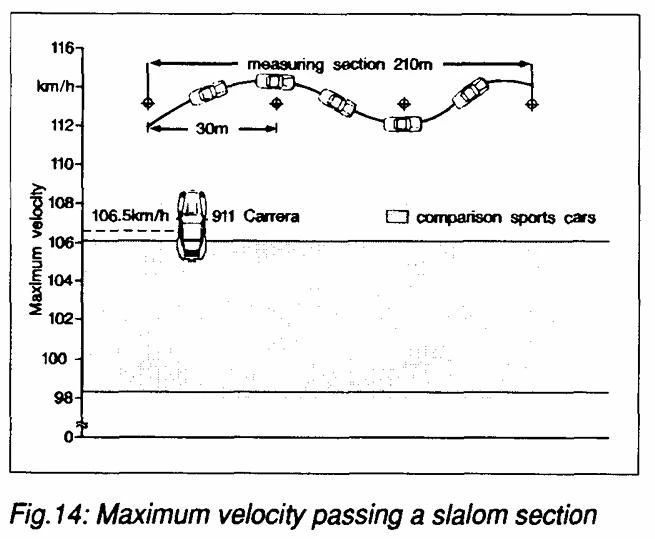
The exceptional stability of the rear suspension is partially attributed to its kinematic and compliant toe variation: toe-in changes occur both during wheel compression (kinematic component) and in response to lateral forces (compliant component). Figure 15 demonstrates this induced toe angle change in the outer rear wheel under lateral acceleration. The resulting understeer effect generated by the rear suspension helps counteract oversteer tendencies.
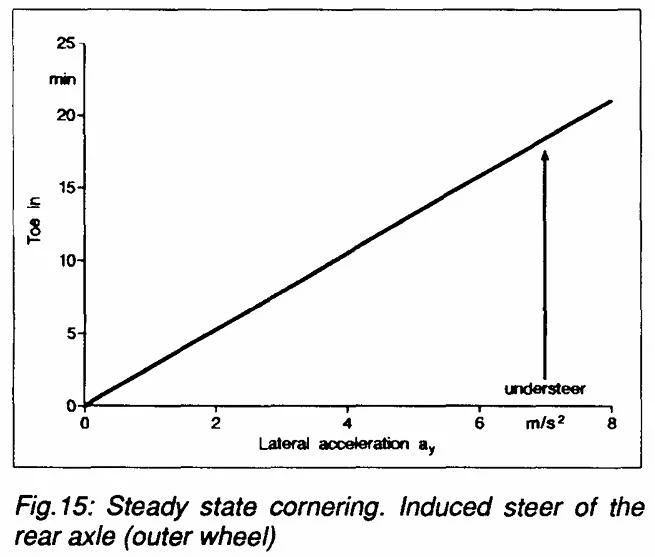
07 Braking System
7.1 Objectives
The braking system (Figure 16) is designed strictly following Porsche’s braking philosophy: it must meet the fundamental requirements of sporty driving, comply with all legal standards, and fulfill everyday driving needs.
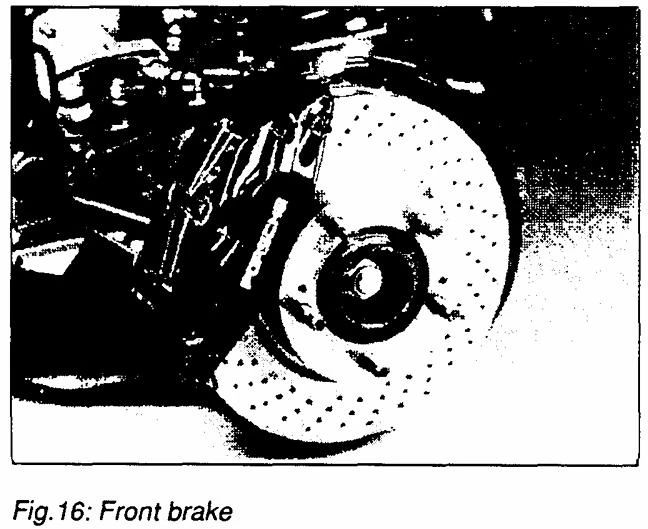
Porsche’s fade resistance test consists of 25 braking cycles, decelerating from 90% of the vehicle’s top speed to 100 km/h with 0.8g deceleration, at intervals corresponding to maximum power output. To pass this test, all influencing factors must be carefully calibrated, including the cooling air system, wheel brake concept, tire dimensions, and anti-lock braking system. These tests yield braking performance values and deceleration times that—even in such high-performance cars—can be multiple times shorter than acceleration times (Figure 17).
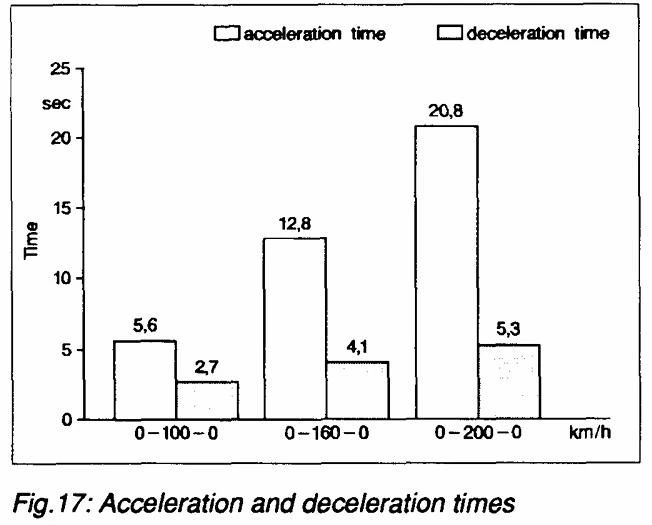
The acceleration test, like the fade resistance test, is a design simulation intended to cover all maximum load conditions—such as timed track driving, extreme downhill braking, or highway driving with permitted gross weight. This test is used during vehicle testing and serves as a computer program to determine the wheel brake system layout.
7.2 Implementation and Characteristics
7.2.1 Brake Hydraulic System
The standard brake hydraulic system includes a 3-channel ABS (Anti-lock Braking System). The optional 4-channel brake system combines ABS with ABD (Automatic Brake Differential). All systems are equipped with wheel speed sensors to optimally monitor each wheel’s speed. The ABS/ABD system is a newly developed unit, making its global debut in the 911 Carrera model.
7.2.2 Wheel Brake System
To align with the braking layout objectives, the entire brake system was adapted to the higher power output of the new-generation high-performance 911. It employs Porsche’s proven 4-piston fixed-caliper concept, which excels in motorsport and has been further developed for enhanced performance and packaging.As a result, the front suspension features a larger brake system from Porsche’s fixed-caliper modular system, with brake discs measuring 32 mm in width, an outer diameter of 304 mm, and a friction pad area of 62.5 cm² per side. Additionally, unsprung mass was reduced by using lightweight alloys where technically and economically feasible.This weight reduction—combined with hard-anodized brake pistons and caliper housings for extended service life—is further enhanced by high-strength, corrosion-resistant copper alloy brake lines, as well as special steel in wear-prone areas like the brake pad guides and retention system.The motorsport-compliant, asbestos-free brake pads ensure maximum fade resistance and wear durability. Both front and rear brake pads are equipped with wear sensors.
7.2.3 Brake Disc Design
The ventilated and perforated brake discs feature:
Specially curved internal cooling vanes
Additional cooling fins on the front discs (derived from racing technology and patent-protected)
High-alloy materials developed for racing applications to prevent thermal distortion, excessive wear, and cracking
A key characteristic of the disc material is its high thermal conductivity. A carbon-saturated structural composition significantly improves resistance to thermal shock cracks while maximizing heat dissipation.
The perforated friction surfaces further enhance heat dissipation. These perforations also reduce wet-road braking response times: steam pressure no longer counteracts pad application force but escapes through the disc openings.
However, achieving fully balanced thermodynamics within the braking system requires additional aerodynamic measures, such as dedicated fresh-air intakes at the vehicle’s front and heat evacuation through lightweight alloy wheels.
The wheel design ensures heated air is extracted at high speeds, while prolonged downhill braking maximizes heat dissipation.
7.4 Brake System Performance
Braking tests compare the Carrera’s system efficiency against other manufacturers. Deceleration from 96 km/h (60 mph) on dry pavement yields ~1.05g (Figure 18), with a stopping distance of 34.5 meters. Other sports/sporty sedans require 36–50 meters, while conventional sedans with less ambitious braking systems may need up to 54 meters.
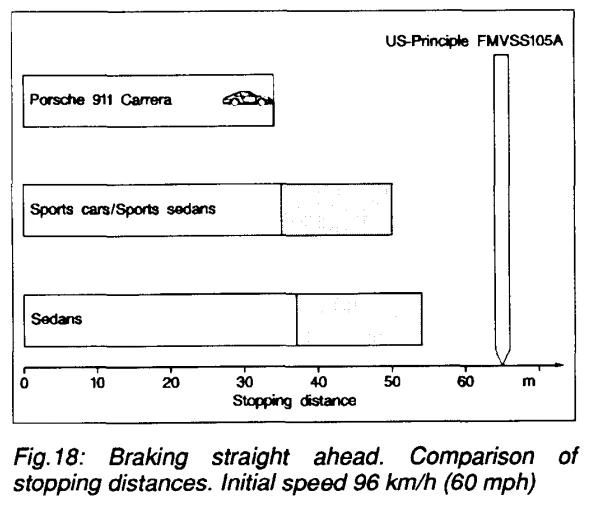
The following mathematical example illustrates what occurs when braking a vehicle from 96 km/h to a complete stop:
The Porsche achieves a braking distance of 34 meters at 1.05g deceleration. Under identical test conditions, vehicles requiring 50 meters to stop would still retain a residual speed exceeding 54 km/h when the Porsche Carrera comes to rest (see Figure 19). Brake systems merely compliant with US FMVSS 105A standards exhibit residual speeds as high as 66 km/h.
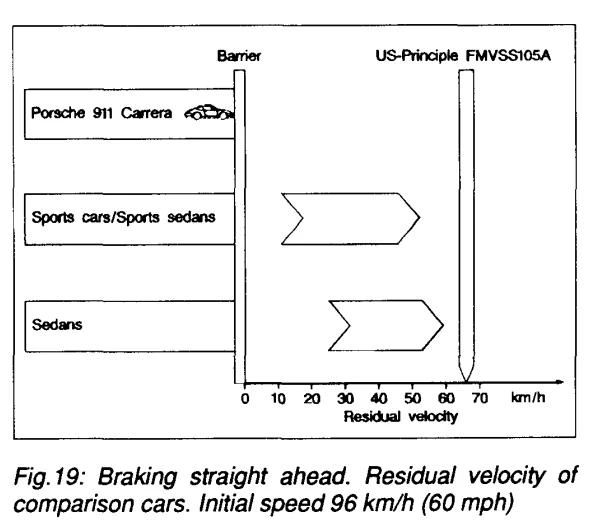
The brake system layout and fade resistance behavior are the main criteria for evaluating braking systems. Thermal fade testing is part of every automaker’s test program and is legally required. However, different automakers use vastly different test methods, making the results nearly incomparable. As mentioned above, Porsche also has its own test method for evaluating brake systems. To obtain comparable results, a known test procedure from literature was applied to the Carrera’s brake system: the car accelerates from standstill to a quarter-mile distance, then brakes at 0.5g deceleration, repeating this process ten times. Figure 20 shows the relationship between brake pedal force and the number of test cycles performed. It can be seen that the measured pedal force remains constant at about 90 newtons, showing absolutely no signs of brake fade under these test conditions.
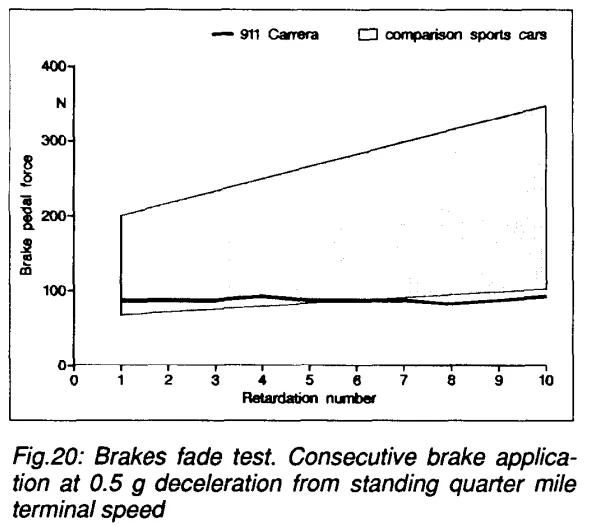
08 Tires and Wheels
Consumers purchasing high-performance sports cars pay special attention to tires and wheels, as they must not only meet visual demands but more importantly technical requirements, since tires represent the most critical contact point between the vehicle and road surface. Under all driving conditions, tires must ensure the following feedback:
※ Lateral forces during cornering
※ Longitudinal forces during acceleration and deceleration
※ Vertical forces
The new Carrera’s chassis is equipped with larger-sized tires and newly developed wheels.
8.1 Objectives
For the slightly more comfortable series chassis and optional sportier configuration models, the following objectives were defined:
Tires
※ Adapt tires to the new chassis
※ Improve rolling resistance
※ Enhance wear resistance
※ Optimize tire adhesion on wet road surfaces
Improve the following driving characteristics:
※ Steering response (steering input, precision, etc.)
※ Lateral stability (primarily adjusting transverse stability between front/rear suspensions)
※ Braking behavior (directional stability, braking distance)
Wheels
※ Use wider wheels for both front and rear suspensions
※ Newly designed lightweight wheels (reducing unsprung mass and rotational mass)
※ Optimized brake ventilation system
8.2 Series Tires
The evolution from Carrera 2 to the new Porsche 911 also involved tire improvements. Table 4 compares the 911’s series wheel and tire sizes with its predecessor’s.
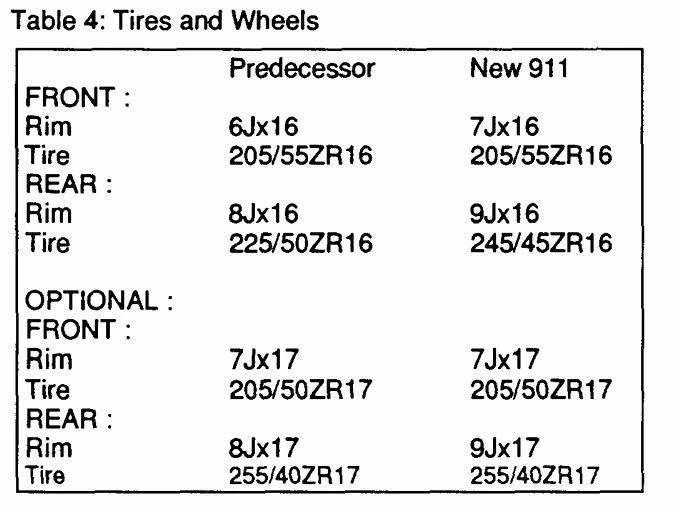
The 911 features wheels that are 1 inch wider on both front and rear axles compared to its predecessor, with rear tires 20 mm wider.
The rear tires offer higher lateral force potential while improving rolling resistance, ride comfort, tire noise, and wear, along with enhanced driving stability.
Despite the rear tires’ increased load capacity, the recommended tire pressure remains unchanged, as lowering it could compromise the rolling resistance improvements.
8.3 Wheels
Both standard and optional wheels have been newly designed and engineered. The 16-inch standard wheels feature rim widths of 7J (front) and 9J (rear). Key development goals were weight savings and improved brake ventilation.
For the 17-inch 911 wheel option, a newly designed 5-spoke wheel was developed, further reducing weight (6 kg per vehicle).
09 Conclusion
In summary, significant efforts were made to further enhance the outstanding performance of the 911 chassis, reflected in its handling characteristics and noticeably improved driving comfort. The new 911 Carrera demonstrates greater agility and stability.
Comparisons with other vehicles show that the new 911 Carrera ranks among the best in its class, with its handling characteristics and braking tests together forming the foundation of excellent active safety.